If a Star Configuration is Unavoidable
페이지 정보

본문
You can easily enjoy the advantages such as low power consumption and long transmission range, without affording the cost of changing the sensors you are using. These advantages compared to other alternatives made RS485 popular and used in a widespread amount of instances. Due to this and it being able to transmit data over long distances, the RS485 is used commonly as a protocol for POS, industrial and telecom. Most Modbus implementations use RS485 due to the allowance of longer distances, higher speeds and multiple devices on a single network. The design of RS485 is targeted towards it being tolerant and forgiving to noise and long cable runs with the twisted pair cable arrangement. Without termination resistors, signal reflections off the unterminated end of the cable can cause data corruption. As a rule of thumb, the speed in bit/s multiplied by the length in metres should not exceed 108. Thus a 50-meter cable should not signal faster than 2 Mbit/s.
Interoperability of even similar devices from different manufacturers is not assured by compliance with the signal levels alone. The other devices (the slaves) respond by giving the requested data to the master, or by taking the action requested in the query. It is optimal for outdoor use cases that need reliable data collected over years. Digital communications networks implementing the standard can be used effectively over long distances and in electrically noisy environments. It is known for being able to be used effectively over long distances and in electrically noisy environments. The aforementioned SenseCAP Sensor Hub at its stock has only 4 ports to connect RS485 sensors despite it being able to support up to 32 different RS485 sensors. Designed to be used with the SenseCAP Sensor Hub, this splitter is able to "split" one MODBUS RS485 port into 4. The RS485 splitter has one male interface that connects to the Sensor Hub and four female interfaces that link to the sensors. Our product was specially designed to provide you with the most complete data about what is happening in your computer at the serial port level in the most convenient way.
All operational algorithms are carefully optimized in order to get the maximum performance, so the real-time solutions based on this product can be appropriate even where any other solution will not give proper results. This means data can be transmitted in both directions to and fro devices one direction at a time. Devices will be linked together via a bus configuration as shown in the picture above. After this, the application will start parsing and decoding all matching packets according to custom protocol definition.Being used with automation tools (Scripting, Serial Terminal, MODBUS Send) it provides you with serial protocol automatic event control handler functionality. The built-in scripting support offers the possibility to control several in-application objects with user-written scripts written in TypeScript (JavaScript superset).Being used with custom protocols parsing feature (Custom visualizers) and Serial Terminal / MODBUS Send it provides you with serial protocol automatic event control handler functionality. Since such set is provided only by our product, it is the only one you can use to create inexpensive automatic testing systems for serial equipment and applications. As you implement serial communications protocols, develop applications or hardware devices, you may need to monitor the data being sent to the ports and interfaces, modify this data, insert delays, and even insert new data packets.
Often, in such cases, you do not have documentation for the device or application and you have to intercept their data, reconstruct communication protocols and individual packets. Manufacturing facilities use serial communication to link their devices together. In the process of development of serial devices there is a necessity of their communication with PC via RS232 ports. This whole system allows manufacturing facilities to control their devices remotely and also set-up automation. RS485 is used as the physical layer for many standards and proprietary automation protocols to implement control systems, most commonly Modbus. This MODBUS Master/Slave device simulator tool provides an easy way to control a MODBUS-compatible device. Our product provides simultaneous data tracking, data parsing (according to any given protocol), data filtering, event processing, packet construction and automation by means of scripting. This means that it is protected from contact with all dust particles, and also high-pressured water jets! This means that data can be simultaneously transmitted and received between devices. Modbus devices communicate using a Master-Slave technique where only one device (the Master) can initiate transactions (AKA queries). Templates can be exported and imported to support various applications. Although many applications use RS-485 signal levels, the speed, format, and protocol of the data transmission are not specified by RS-485.
If you cherished this posting and you would like to obtain more details about what is rs485 cable kindly stop by our own web-page.
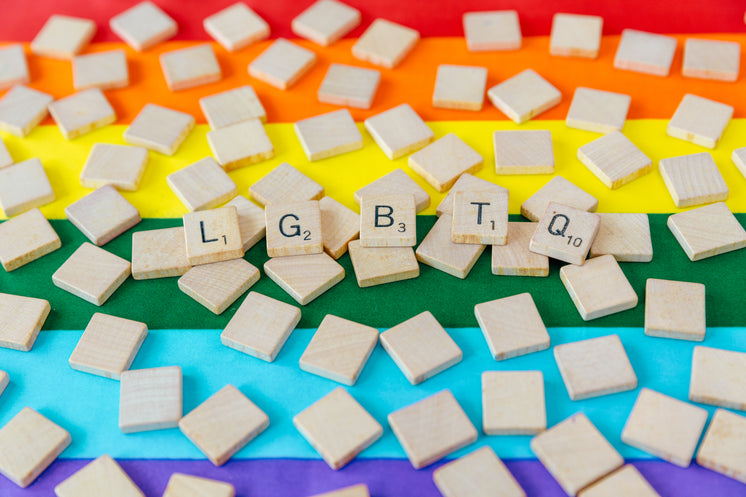
- 이전글pobieranie z instagrama 980 24.07.26
- 다음글9 Lessons Your Parents Taught You About Lightest Double Stroller 24.07.26
댓글목록
등록된 댓글이 없습니다.